Optimizing Facility Maintenance with Effective CMMS Software Utilization
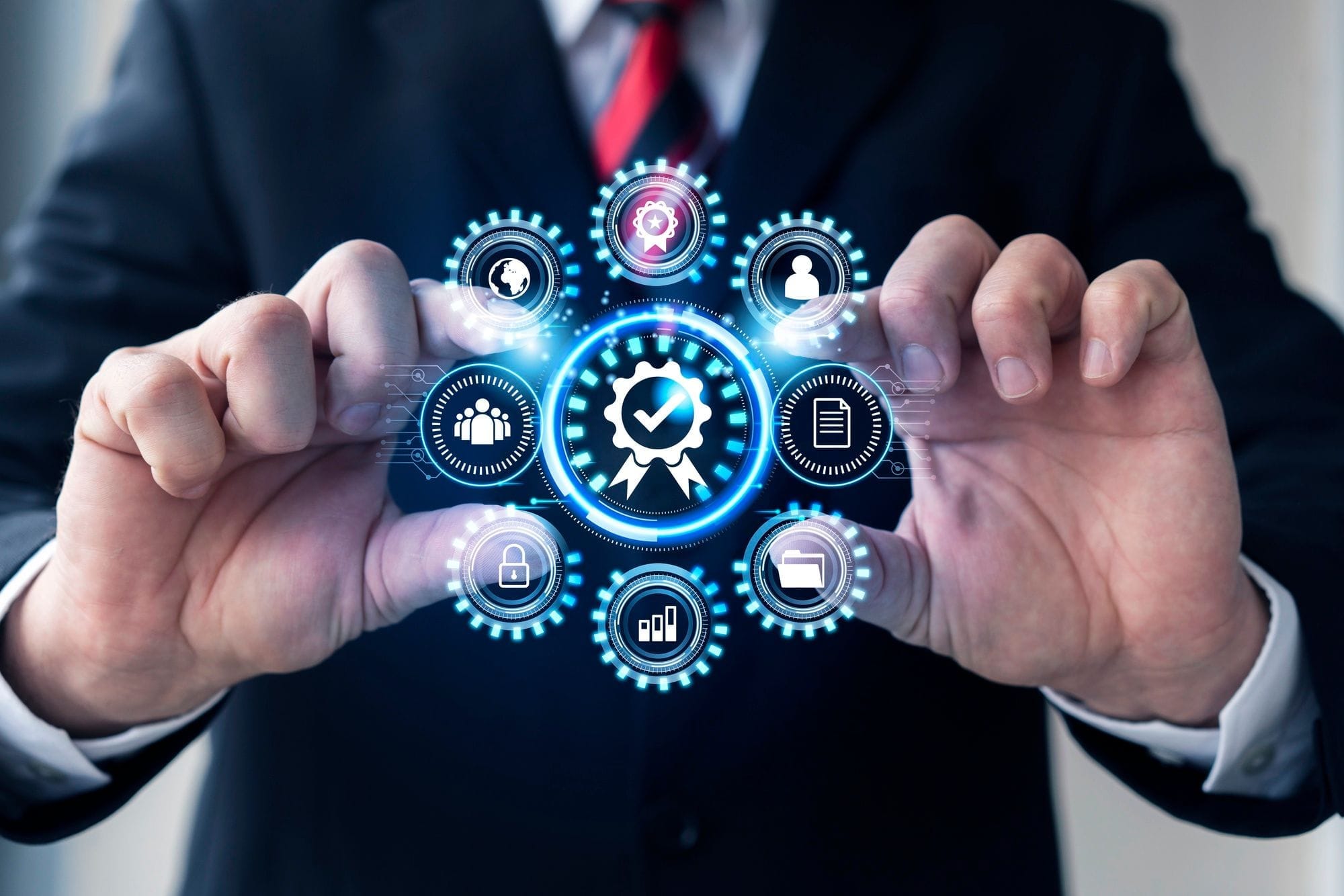
Effectively using a Computerized Maintenance Management System (CMMS) software can greatly enhance a facility manager's ability to streamline maintenance operations, track assets, and make data-driven decisions. Here are steps and best practices for facility managers to effectively use CMMS software:
Select the Right CMMS Software:
Start by choosing a CMMS software that aligns with your facility's specific needs, size, and industry. Ensure it offers the features and scalability required for your maintenance operations.
Data Input and Asset Management:
Begin by inputting all relevant data into the CMMS software. This includes creating a comprehensive list of assets, equipment, and systems within the facility. Each asset should have a unique identifier and associated details, such as manufacturer, model, and warranty information.
Set Up Preventive Maintenance (PM) Tasks:
Utilize the CMMS software to schedule and manage preventive maintenance tasks. Define maintenance schedules, inspection intervals, and associated checklists for each asset. This ensures that maintenance is performed at regular intervals to prevent breakdowns.
Work Order Management:
Use the CMMS to create and manage work orders. When issues or breakdowns occur, generate work orders to assign tasks to maintenance personnel. Include details such as the nature of the problem, priority level, required materials, and due dates.
Inventory and Spare Parts Management:
Keep track of spare parts and inventory within the CMMS. Monitor stock levels, reorder thresholds, and consumption rates. The system can generate purchase orders for restocking when inventory falls below a specified level.
Asset Histories and Documentation:
Maintain detailed records of maintenance activities for each asset. This includes documenting repairs, inspections, parts replacements, and associated costs. Having a comprehensive asset history helps in making informed decisions about repairs and replacements.
Mobile Accessibility:
Many modern CMMS software solutions offer mobile apps or web-based interfaces that allow maintenance teams to access and update information in real-time from smartphones or tablets. This can improve communication and efficiency.
Integration with Sensors and IoT Devices:
If applicable, integrate the CMMS software with sensors and IoT (Internet of Things) devices installed on critical equipment. This enables real-time monitoring of equipment health and can trigger maintenance tasks automatically when anomalies are detected.
Generate Reports and Analytics:
Utilize the reporting and analytics capabilities of the CMMS to gain insights into maintenance performance. Generate reports on key metrics such as equipment downtime, maintenance costs, and work order completion rates. Use these insights to identify areas for improvement.
Training and User Adoption:
Ensure that maintenance personnel are trained to use the CMMS effectively. Encourage user adoption by demonstrating the software's benefits in terms of time savings, reduced paperwork, and improved maintenance efficiency.
Continuous Improvement:
Regularly review and refine your maintenance processes based on the data and insights provided by the CMMS software. Identify trends, patterns, and areas where preventive maintenance can be optimized.
Security and Data Backups:
Implement robust security measures to protect sensitive maintenance data stored in the CMMS. Regularly back up data to prevent loss in case of system failures or data breaches.
Compliance and Documentation:
Use the CMMS to maintain records related to compliance with regulatory requirements, safety standards, and environmental regulations. Ensure that all necessary documentation is easily accessible.
Feedback and Communication:
Encourage feedback from maintenance teams on the usability and effectiveness of the CMMS software. Continuously communicate with team members to address any challenges and make necessary improvements.
Vendor Support and Updates:
Stay in touch with the CMMS software vendor for updates, patches, and technical support. Ensure that you are using the latest version of the software to benefit from new features and security enhancements.
In summary, effective use of CMMS software involves proper setup, asset management, preventive maintenance scheduling, work order management, data analysis, and continuous improvement. By leveraging the capabilities of CMMS software, facility managers can enhance maintenance efficiency, reduce downtime, control costs, and ultimately ensure that their facilities operate smoothly and reliably.

For Effective Facility Maintenance, Get started now with the Mobile First CMMS App.