Your Preventive Maintenance Plan Might Be Failing – Here’s How to Fix It
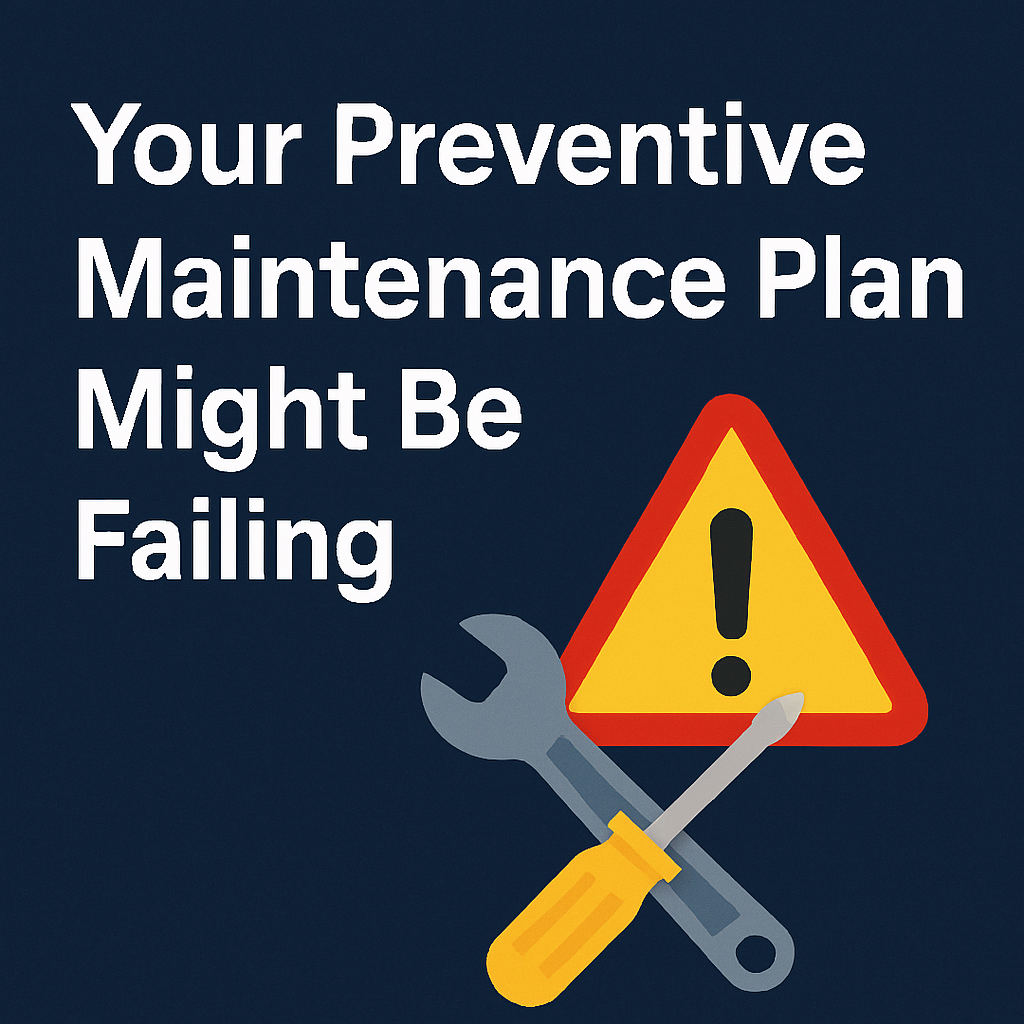
Preventive maintenance (PM) is the bedrock of any efficient and reliable operation. The goal is simple: perform scheduled maintenance tasks to prevent unexpected equipment failures, extend asset life, reduce costly downtime, and ensure safety. But what happens when, despite having a PM plan on paper, you're still battling frequent breakdowns and spiraling repair costs?
Your preventive maintenance plan might be failing.
It's a common problem. Many organizations invest time setting up a PM schedule, only to find it doesn't deliver the expected results. It becomes a box-ticking exercise rather than a strategic tool for reliability. Recognizing the signs of a failing plan is the first step toward fixing it.
Signs Your PM Plan Isn't Working:
- Frequent Unexpected Breakdowns: If equipment that's supposedly covered by your PM schedule is still failing unexpectedly, your plan isn't preventing the issues it should.
- Rising Maintenance Costs: While PM involves upfront costs, it should reduce overall maintenance expenses by preventing major, expensive repairs. If your total costs (labor, parts, downtime) are climbing, something's wrong.
- PM Tasks Feel Rushed or Skipped: Technicians might be cutting corners or skipping tasks altogether due to unrealistic schedules, lack of parts, insufficient time, or unclear instructions.
- Lack of Data and Insight: You can't manage what you don't measure. If you don't have clear data on PM completion rates, failure trends, or maintenance costs per asset, you're flying blind.
- Equipment Not Reaching Expected Lifespan: Consistently replacing assets before their manufacturer-estimated lifespan is a major red flag.
- Low Technician Morale/Buy-in: If your team sees the PM plan as pointless "busy work" rather than valuable maintenance, their engagement and the quality of work will suffer.
Why Do PM Plans Fail? Common Causes:
- Generic or Outdated Plans: Using manufacturer recommendations without tailoring them to your specific operating conditions, asset age, or failure history. What worked five years ago might not be optimal today.
- Poor Scheduling and Resource Allocation: Not scheduling PM effectively, leading to conflicts, insufficient time for tasks, or unavailability of necessary parts and tools.
- Lack of Specificity: Vague task descriptions ("Check motor") leave too much room for interpretation and inconsistency.
- Insufficient Training: Technicians may lack the specific skills or knowledge needed to perform PM tasks correctly.
- Inadequate Data Tracking and Analysis: Relying on paper or basic spreadsheets makes it incredibly difficult to track compliance, analyze trends, and optimize the plan based on real-world performance.
- Ignoring Condition Monitoring: Relying solely on time-based PM instead of incorporating condition-based monitoring (vibration analysis, thermography, oil analysis) where appropriate.
How to Fix Your Failing PM Plan:
Fixing a failing PM plan requires a shift from a static checklist approach to a dynamic, data-driven strategy.
- Audit and Optimize Your Tasks:
- Review every PM task. Is it necessary? Is the frequency correct? Is it addressing known failure modes?
- Involve your technicians – they have valuable hands-on insights.
- Prioritize tasks based on asset criticality and failure risk. Not all equipment needs the same level of attention.
- Update tasks based on failure history, operating conditions, and (if available) condition monitoring data.
- Improve Scheduling and Resource Planning:
- Ensure realistic time estimates for tasks.
- Coordinate PM schedules with production to minimize disruption.
- Implement kitting – ensure necessary parts, tools, and instructions are ready before the technician starts the job.
- Balance workloads among technicians.
- Standardize Procedures and Enhance Training:
- Develop clear, step-by-step instructions for each PM task. Include checklists and safety warnings.
- Provide ongoing training to ensure technicians have the necessary skills.
- Explain the why behind PM tasks to improve buy-in.
- Embrace Data: Implement a CMMS:
- This is arguably the most impactful step. Manual systems are prone to errors, lost information, and make analysis nearly impossible.
- A Computerized Maintenance Management System (CMMS) centralizes all your maintenance data – asset information, work order history, PM schedules, parts inventory, labor hours, and costs.
- It automates scheduling, sends reminders, provides mobile access for technicians, and generates reports on key performance indicators (KPIs) like PM compliance, Mean Time Between Failures (MTBF), and overdue work.
- Analyze and Continuously Improve:
- Regularly review your maintenance KPIs generated by your CMMS.
- Analyze failure data – what's breaking, why, and how often? Use this information to adjust PM tasks and frequencies.
- Treat your PM plan as a living document, subject to ongoing refinement based on performance data.
Leveraging Technology for Success:
Implementing these fixes, especially data tracking and optimized scheduling, can feel overwhelming with manual systems. This is where technology becomes essential. A modern, user-friendly CMMS like www.maintainnow.app provides the tools you need to effectively manage your entire maintenance operation.
With a solution like MaintainNow, you can:
- Easily schedule and track PM tasks.
- Store detailed asset histories and documentation.
- Manage work orders digitally, from creation to completion.
- Track labor and parts costs accurately.
- Generate insightful reports to identify trends and optimize your strategy.
- Empower technicians with mobile access to information and task lists.
Conclusion:
A failing preventive maintenance plan isn't just ineffective; it's actively costing you money and increasing operational risk. By recognizing the warning signs, understanding the root causes, and taking decisive steps to optimize – particularly by leveraging the power of a robust CMMS likewww.maintainnow.app– you can transform your PM program from a liability into a powerful driver of reliability, efficiency, and profitability. Don't let your PM plan fail silently; take action today to ensure it delivers the results you need.