Work Orders:The Key to Efficient Facility Maintenance
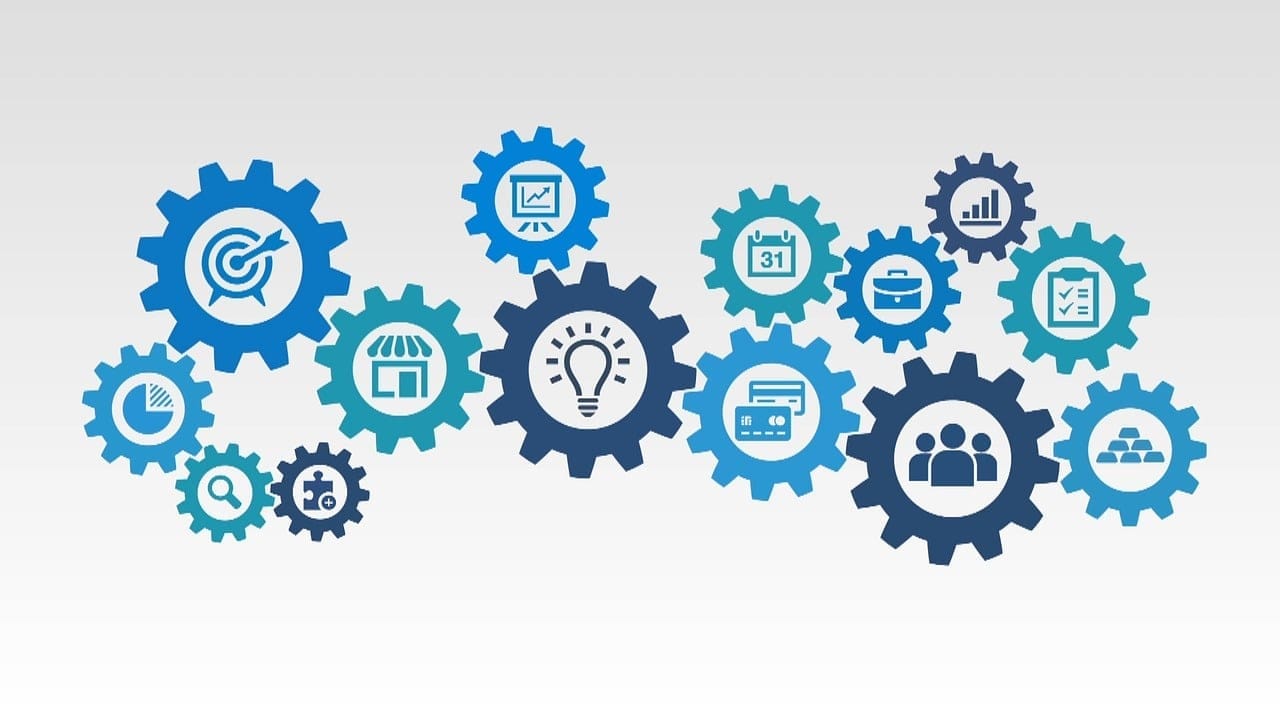
Facility maintenance is a critical aspect of ensuring the smooth and safe operation of any organization's physical assets. Whether you're managing a commercial building, a manufacturing plant, or a healthcare facility, proactive and organized maintenance is essential to prevent costly breakdowns, ensure compliance with regulations, and extend the lifespan of your equipment and infrastructure. One of the cornerstone tools in effective facility maintenance is the work order.
What Is a Work Order?
A work order is a formal document or request that outlines a specific maintenance task or job that needs to be performed. It serves as a roadmap for facility managers, maintenance teams, and technicians, providing essential details about the task at hand. A well-crafted work order includes information such as:
- Task Description: A clear and concise description of the maintenance task or repair needed.
- Location: The specific area or asset where the work is to be performed.
- Priority: The urgency and importance of the task, helping managers prioritize workloads.
- Resources: The labor, materials, tools, and equipment required for the job.
- Scheduling: Start and end dates for the task, ensuring efficient allocation.
- Assigned Personnel: The individuals or teams responsible for completing the work.
The Role of Work Orders in Facility Maintenance
Work orders play a pivotal role in efficient facility maintenance in several ways:
1. Task Organization: Work orders provide structure and clarity to maintenance tasks. They eliminate ambiguity, ensuring that everyone involved understands the scope and requirements of the job.
2. Priority Management: Facility managers can assign priorities to work orders, ensuring that critical maintenance tasks receive immediate attention. This helps minimize downtime and mitigate potential safety hazards.
3. Resource Allocation: By detailing the necessary resources, work orders assist in resource allocation. This prevents overallocation or shortages of labor, materials, and equipment.
4. Accountability: Work orders assign responsibility for each task, promoting accountability among maintenance teams and contractors. This accountability ensures that work is completed on time and to the required standards.
5. Documentation: Work orders serve as a historical record of maintenance activities. This documentation is invaluable for compliance, audits, and warranty claims, as it provides a comprehensive history of work performed.
6. Cost Tracking: By recording expenses associated with each work order, facility managers can accurately track maintenance costs. This information is vital for budgeting and cost control.
7. Preventive Maintenance: Work orders are also instrumental in scheduling and managing preventive maintenance tasks. Regular inspections and servicing of equipment and facilities can prevent breakdowns and extend their lifespan.
8. Data Analysis: Over time, data collected from work orders can be analyzed to identify trends, recurring issues, and areas for improvement in facility maintenance processes.
Conclusion
In the field of facility maintenance, work orders are an indispensable tool for efficient and organized operations. They streamline processes, reduce costs, enhance safety, and extend the life of assets. Modern computerized maintenance management systems (CMMS) have revolutionized work order management by automating and optimizing the process, making it even more effective.
