Various Types of Maintenance
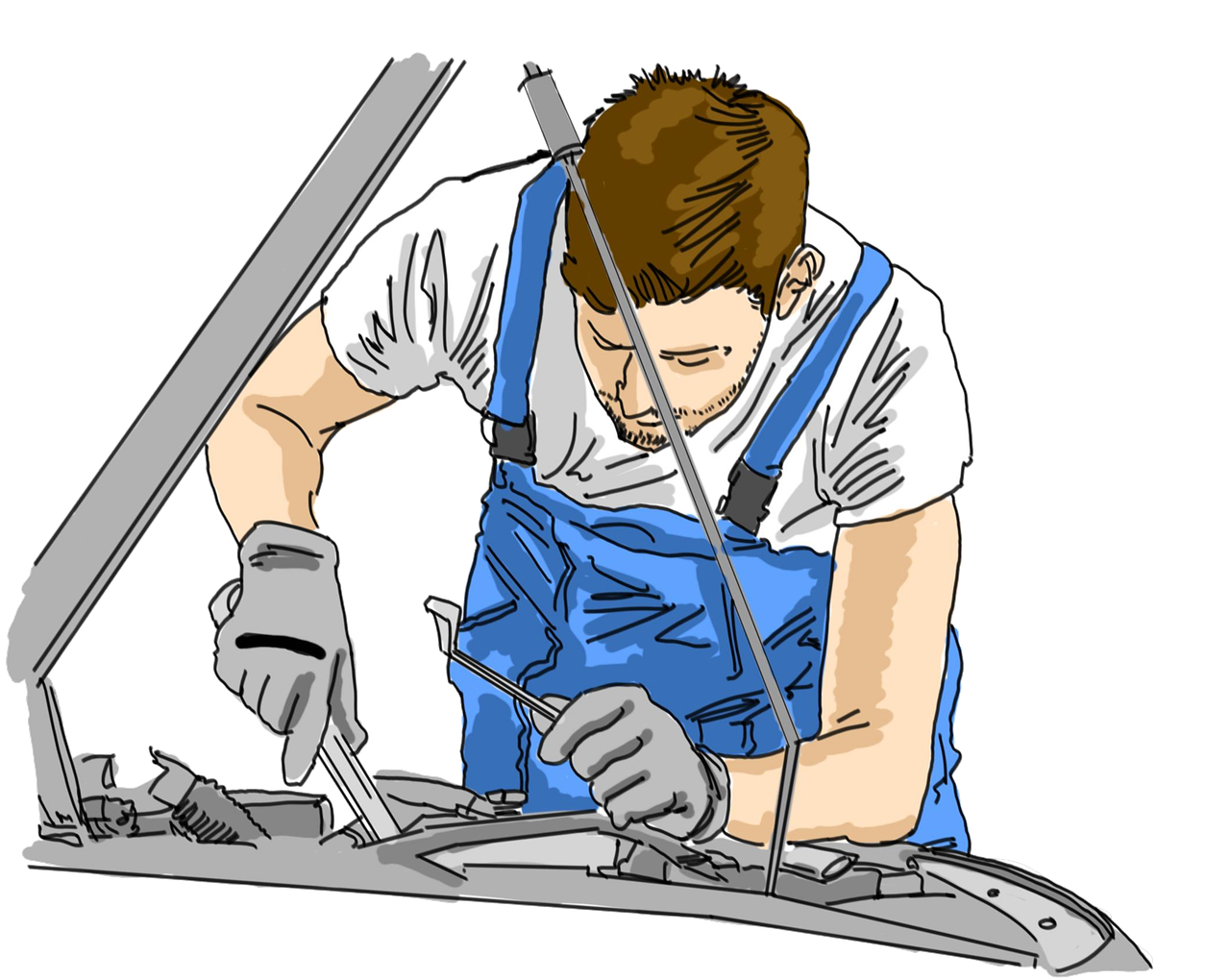
In the ever-evolving landscape of maintenance practices, numerous methods have emerged to ensure the smooth operation of equipment and assets. These methods range from reactive approaches to proactive strategies, each with its unique characteristics and applications. Let's delve into the world of maintenance methods with this comprehensive article, presented in bullet points for easy reference:
1. Run-to-Failure
- Oldest type of maintenance.
- Suitable for small, non-critical, low-priced equipment.
2. Corrective Maintenance
- Unplanned activities to restore equipment to its operating condition.
3. Scheduled Maintenance
- Periodic replacement of parts based on their age.
- Planned basis for maintenance activities.
4. Preventive Maintenance
- Encompasses planned, scheduled, and corrective actions taken before equipment failure occurs.
5. Condition-Based Maintenance (CBM)
- Relies on objective evidence or predictable failure for systems or components.
- Includes scheduled and corrective maintenance.
- Utilizes various technologies for objective evidence.
6. Condition Monitoring
- Maintenance without preventive tasks.
- Equipment remains in service until functional failure occurs.
7. Predictive Condition Monitoring (PCM)
- Combines multiple technologies to monitor machine conditions.
- Tracks various conditions and performance measurements to predict failures.
8. Equipment Asset Management
- Combines best practices, technology, organization, and administration for maximizing equipment lifetime value.
9. Reliability-Centered Maintenance (RCM)
- Determines maintenance requirements in the context of a physical asset's operation.
- Ensures assets fulfill their functions effectively.
10. Preactive Maintenance
- Defines maintenance requirements before processes or machines commence operation or undergo expansion.
11. Total Productive Maintenance (TPM)
- Involves plant operators, safety, energy, materials, and quality in maintenance efforts.
- Aims to improve overall plant performance.
12. TQMain
- Strategy for monitoring and controlling process conditions and product quality.
- Detects failure causes and potential issues for timely intervention.
13. Productive Reliability (PR)
- Based on TPM methodology.
- Focuses on reducing costs and enhancing capacity through continuous maintenance improvements.
14. Operating Maintenance Training and Administration
- Holistic approach considering all aspects of infrastructure.
- Integrates operation, maintenance, training, and administration as integral parts of the system.
15. Proactive Maintenance (PaM)
- Advanced approach aiming to minimize maintenance needs and maximize machinery lifespan.
- Enhances preventive and predictive maintenance practices.
16. Profit Center Maintenance
- Considers maintenance of machinery and equipment as a profit activity.
- Optimizes for maximum value, not just minimal cost.
17. Maintenance Management Metric
- Involves allocating value-added resources to improve overall equipment effectiveness while optimizing per-unit production costs.
18. Other Maintenance Methods
- Include machinery reliability management, total plant performance maintenance, optimized asset utilization, asset utilization, and economic value-added.
The ever-expanding repertoire of maintenance methods underscores the importance of adapting strategies to specific needs and conditions. From the traditional run-to-failure to cutting-edge predictive condition monitoring, organizations must carefully choose the approach that best aligns with their goals and assets. Ultimately, effective maintenance ensures equipment longevity, optimal performance, and cost-efficiency in today's fast-paced industrial landscape.
