The Secret to 99% Uptime: What High-Performing Facilities Are Doing Differently
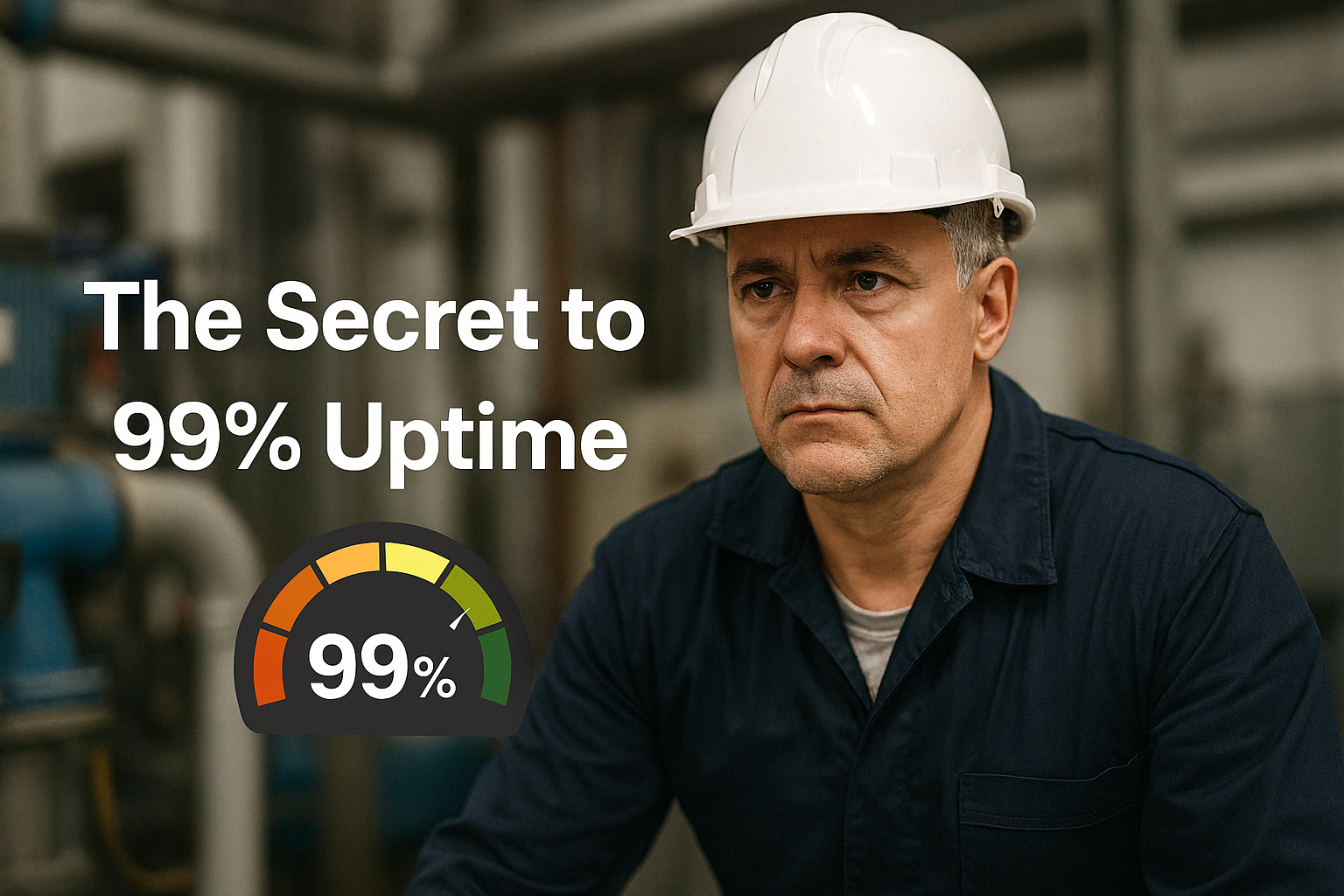
In today's competitive landscape, unplanned downtime is the enemy. It disrupts production, frustrates customers, and eats away at your bottom line. While achieving 100% uptime might seem like a mythical creature, a remarkable 99% is within reach. So, what separates the facilities consistently hitting this benchmark from the rest? It's not magic; it's a set of proactive strategies and a commitment to operational excellence. Let's delve into the key differences:
1. They Embrace Proactive Maintenance, Not Just Reactive Firefighting:
The most significant differentiator is their approach to maintenance. Instead of waiting for equipment to fail and then scrambling to fix it (reactive maintenance), high-performing facilities prioritize preventive and predictive maintenance.
- Preventive Maintenance: Regularly scheduled tasks like inspections, lubrication, and component replacements based on time or usage intervals. This catches potential issues early, preventing minor problems from escalating into costly breakdowns.
- Predictive Maintenance: Utilizing data and technology to monitor equipment condition and predict when maintenance is needed. This could involve vibration analysis, thermal imaging, oil analysis, and other advanced techniques. This targeted approach optimizes maintenance efforts, addressing issues only when necessary.
2. Data is Their Guiding Star:
These top-tier facilities don't rely on guesswork. They meticulously collect and analyze data related to their assets, maintenance activities, and overall performance. This data provides valuable insights into:
- Equipment Reliability: Identifying assets that are prone to failure.
- Maintenance Effectiveness: Evaluating the success of different maintenance strategies.
- Resource Allocation: Optimizing the deployment of maintenance personnel and resources.
By understanding their data, they can make informed decisions that directly impact uptime.
3. They Have Streamlined Workflows and Processes:
Efficiency is paramount. High-performing facilities have well-defined workflows for all maintenance tasks, from work order creation to completion and reporting. This ensures:
- Faster Response Times: When issues do arise, they are addressed quickly and efficiently.
- Consistency: Standardized procedures ensure that maintenance is performed correctly every time.
- Accountability: Clear roles and responsibilities are defined for each step of the process.
4. Their Teams are Highly Skilled and Empowered:
They recognize that their maintenance team is their first line of defense against downtime. These facilities invest in:
- Comprehensive Training: Equipping their technicians with the knowledge and skills to perform their jobs effectively.
- Clear Communication Channels: Fostering an environment where team members can easily share information and collaborate.
- Empowerment: Giving technicians the autonomy to identify and address potential problems proactively.
5. They Leverage the Power of Technology:
Modern technology plays a crucial role in achieving high uptime. This is where a robust Computerized Maintenance Management System (CMMS) becomes indispensable. A CMMS app enables facilities to:
- Schedule and Track Preventive Maintenance: Automate the creation and assignment of recurring maintenance tasks, ensuring nothing gets missed.
- Manage Work Orders Efficiently: Streamline the entire work order lifecycle, from request to completion and approval.
- Centralize Asset Information: Store critical details about each asset, including maintenance history, manuals, and warranty information.
- Collect and Analyze Data: Track key performance indicators (KPIs) like mean time between failures (MTBF) and mean time to repair (MTTR) to identify areas for improvement.
- Improve Communication and Collaboration: Provide a central platform for maintenance teams to communicate, share updates, and access information.
- Implement Predictive Maintenance Strategies: Integrate with condition monitoring tools to trigger maintenance based on real-time data.
The Bottom Line:
Achieving 99% uptime isn't about luck; it's about adopting a proactive, data-driven, and technology-enabled approach to facility maintenance. By implementing the strategies outlined above, and leveraging the power of a CMMS app like MaintainNow, your facility can significantly reduce downtime, improve efficiency, and ultimately boost your bottom line.
Ready to take control of your facility's uptime? Visit MaintainNow to learn more!
By the way, I noticed Web & App Activity isn't currently enabled for this Google account. Turning on Web & App Activity in your My Google Activity page would allow me to give more tailored and useful responses in the future.