Smart Inventory Assistant: The Silent Hero of Maintenance Efficiency
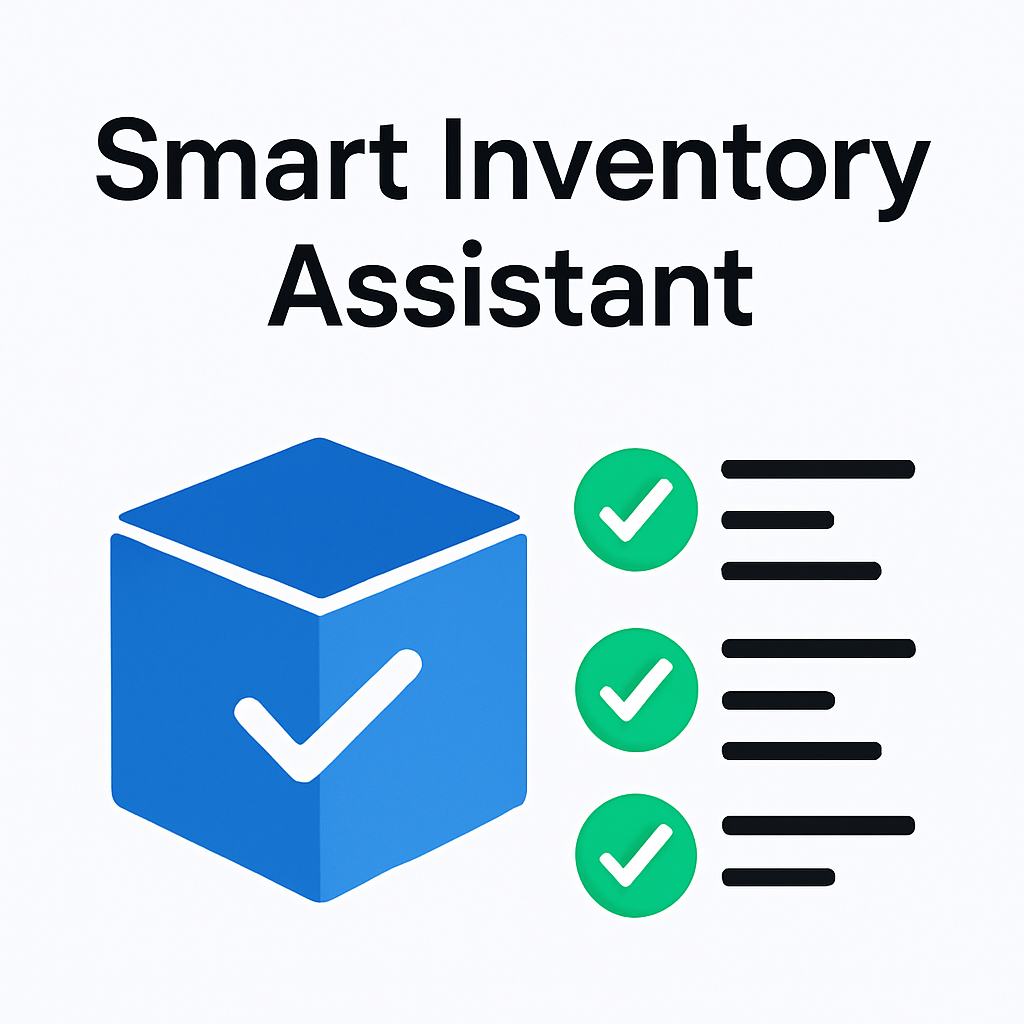
Facility and maintenance managers juggle a million tasks daily — from urgent work orders to compliance checks and labor scheduling. But among all these moving parts, there’s one critical area that quietly determines whether things run smoothly or fall apart: Inventory Management.
Let’s be honest. Most inventory systems are either too basic, too manual, or completely disconnected from the realities of a modern maintenance operation. Enter the game-changer: the Smart Inventory Assistant.
🔋 Why Traditional Inventory Management Falls Short
Facility teams often struggle with:
- Overstocking "just in case," tying up capital and space
- Understocking critical parts, causing costly downtime
- No real-time visibility into what's available and where
- Manually creating reorders (often at the last minute)
- Guesswork in forecasting part usage
The result? Stress, delays, and inefficient spending.
💡 Meet the Smart Inventory Assistant
Imagine having a digital assistant that:
- Monitors your inventory in real-time
- Predicts what you’ll need before you run out
- Sends smart alerts (not just basic low-stock warnings)
- Automatically creates purchase requests
It's like having an extra team member who never sleeps, never forgets, and actually understands your maintenance patterns.
🔍 Key Features
✅ 1. Dynamic Reorder Predictions
Goes beyond static min/max thresholds by learning from:
- Usage frequency by asset or season
- Historical work order trends
- Vendor lead times and shipping delays
✅ 2. Work Order Intelligence
Connects directly to your CMMS work orders to forecast part needs based on:
- Scheduled PMs
- Recurring repairs
- Failure patterns
✅ 3. Smart Alerts & Recommendations
Instead of bland "Stock Low" messages, you get:
- "Reorder 5 belts now to meet projected need for next 30 days"
- "You haven’t used this valve in 12 months — consider deprecating it"
✅ 4. Auto-Replenishment Triggers
The assistant can:
- Auto-generate POs or reorder requests
- Integrate with vendor APIs
- Track pending deliveries and flag delays
✅ 5. Inventory Heat Maps
Visualize fast-moving, obsolete, and critical items across your storeroom with color-coded maps for smarter stocking decisions.
🤖 Future-Ready Enhancements
- IoT Smart Bins: Use weight sensors or RFID to auto-update stock levels.
- Vendor Price Bots: Monitor price trends and suggest cheaper suppliers.
- Field Scan-to-Suggest: Scan a part QR code and auto-link it to related assets or previous work orders.
📊 Why Facility Managers Love It
Benefit | Impact |
---|---|
❌ No Stockouts | Faster repair times, less stress |
📉 Less Waste | Avoid over-ordering and obsolescence |
⏱️ Time Savings | Automated tracking and ordering |
📊 Better Decisions | Real-time data and usage forecasting |
⚙️ CMMS Integration | One system, total visibility |
🛠️ Smart Inventory Inside MaintainNow
MaintainNow is built to support forward-thinking features like the Smart Inventory Assistant. Our platform already integrates asset data, PMs, and work orders — meaning predictive inventory is just a natural next step.
Want to see this in action? Let’s talk.
Final Thought: Inventory might not be glamorous, but when it's smart, it becomes the backbone of reliable, stress-free maintenance. The Smart Inventory Assistant helps you plan ahead, act fast, and stay in control — automatically.