Smart Maintenance Strategies
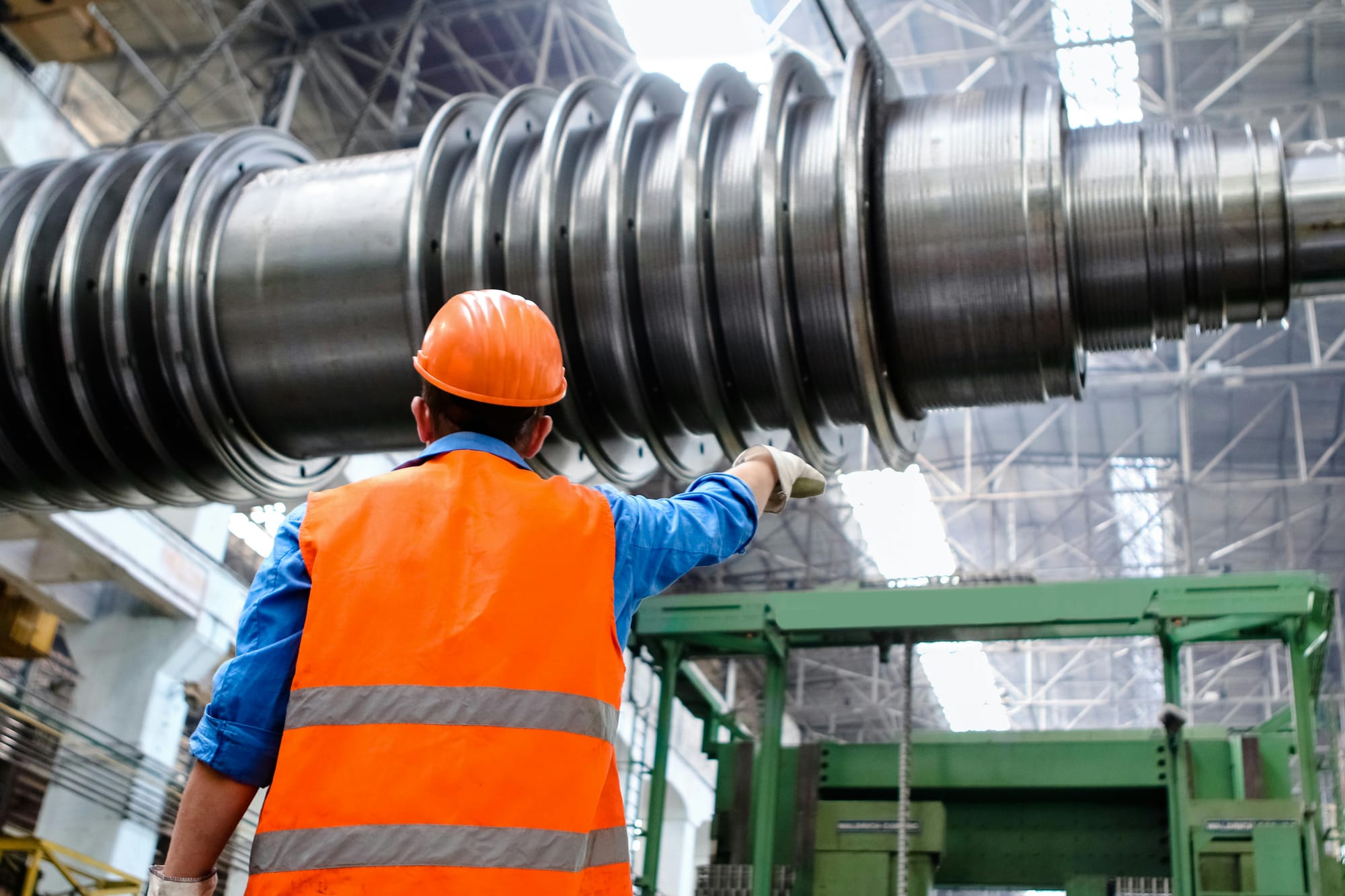
Maintenance management (MM) has evolved significantly over the past decades due to advancements in technology, increased competition, and the need for cost-effective strategies. Effective maintenance ensures equipment reliability, reduces downtime, and enhances overall operational efficiency. The field of maintenance engineering (ME) integrates statistical and operational research techniques to optimize maintenance policies, predict failures, and enhance system reliability.
This article explores the key aspects of maintenance management, focusing on optimization strategies, financial considerations, and organizational techniques.
1. Optimizing Maintenance Policies
To develop an effective maintenance strategy, organizations must analyze system reliability, financial implications, and maintenance models. The optimization process can be divided into the following key areas:
1.1 Reliability and Availability Analysis
- Maintenance decisions rely on data about failure rates, repair times, and preventive maintenance (PM) durations.
- Failure rates can be gathered from:
- Public reliability databanks
- Actual plant performance data
- Expert judgments
- Laboratory testing
- However, reliability databanks often lack details about environmental and operational factors affecting failures.
1.2 Data Quality Challenges
- Many sources present only average failure rates, which may not reflect real-world conditions.
- Environmental factors such as temperature, humidity, and workload can significantly impact failure rates but are often not included in standard databases.
- Organizations should supplement databank information with real-world operational data for better decision-making.
1.3 Laboratory and Field Testing
- Engineers conduct laboratory testing to estimate component lifetimes.
- When full testing is not feasible due to cost or time constraints, organizations use censored data (incomplete test data).
- Real-world plant data must be carefully analyzed to ensure consistency and relevance to specific failure modes.
1.4 Financial Aspects of Maintenance
- Maintenance decisions should balance reliability improvement with cost-effectiveness.
- Key financial factors to consider:
- Direct maintenance costs (labor, spare parts, tools)
- Engineering and administration costs
- Production downtime and lost revenue
- Safety and environmental risks
- Example: A preventive maintenance strategy may reduce unexpected failures but could lead to excessive costs if performed too frequently.
1.5 Maintenance Optimization Models
Various mathematical models help determine the best maintenance policies. These include:
- Time-based maintenance models: Scheduling maintenance at fixed intervals.
- Condition-based maintenance models: Performing maintenance when performance metrics indicate potential failure.
- Optimization models: Using statistical methods (e.g., linear programming, dynamic programming, and stochastic models) to find the best trade-off between costs and reliability.
Despite their theoretical benefits, many optimization models remain underutilized in practice due to difficulties in real-world data collection and system complexity.
2. Organizational Techniques for Maintenance Management
Modern maintenance organizations require flexibility, collaboration, and effective data management to ensure long-term success. The traditional centralized maintenance model is evolving into more decentralized approaches.
2.1 Centralized vs. Decentralized Maintenance
- Centralized maintenance: All maintenance activities are managed from a single department, ensuring consistency but reducing flexibility.
- Decentralized maintenance: Maintenance tasks are distributed across different departments or production areas, increasing responsiveness but requiring better coordination.
- A hybrid approach often works best, allowing a balance between standardization and operational flexibility.
2.2 Workforce Development
- Organizations should invest in multi-skilled technicians to improve efficiency.
- Small workgroups enhance teamwork and communication.
- Cross-functional teams (e.g., maintenance and production teams working together) help improve reliability.
2.3 Communication and Coordination
- Computerized Maintenance Management Systems (CMMS) help track maintenance activities, schedule repairs, and analyze failure trends.
- Enterprise Resource Planning (ERP) integration ensures that maintenance planning aligns with broader business objectives.
2.4 External Relationships and Collaboration
- Maintenance teams should build strong relationships with Original Equipment Manufacturers (OEMs) for reliable equipment support.
- Customers and suppliers should share maintenance-related data to enhance product quality and reliability.
- Strategic outsourcing decisions should be based on long-term business needs rather than cost alone.
3. Future Research and Emerging Trends
New advancements in e-maintenance, IoT-based condition monitoring, and AI-driven predictive maintenance are shaping the future of maintenance management.
Key Research Areas
- E-maintenance frameworks: Integrating cloud-based maintenance solutions.
- Predictive maintenance models: Combining real-time sensor data with failure prediction algorithms.
- Customizable maintenance structures: Adapting maintenance organizations to evolving business strategies.
Conclusion
Optimizing maintenance management requires a combination of data-driven decision-making, financial evaluation, and organizational flexibility. By leveraging statistical analysis, maintenance models, and modern IT solutions, businesses can minimize downtime, reduce costs, and enhance equipment reliability. However, real-world implementation remains challenging due to data limitations and system complexity. Organizations must continuously refine their maintenance strategies by integrating new technologies and adapting to operational changes.