Maximizing Asset Management Excellence: The Size of the Prize
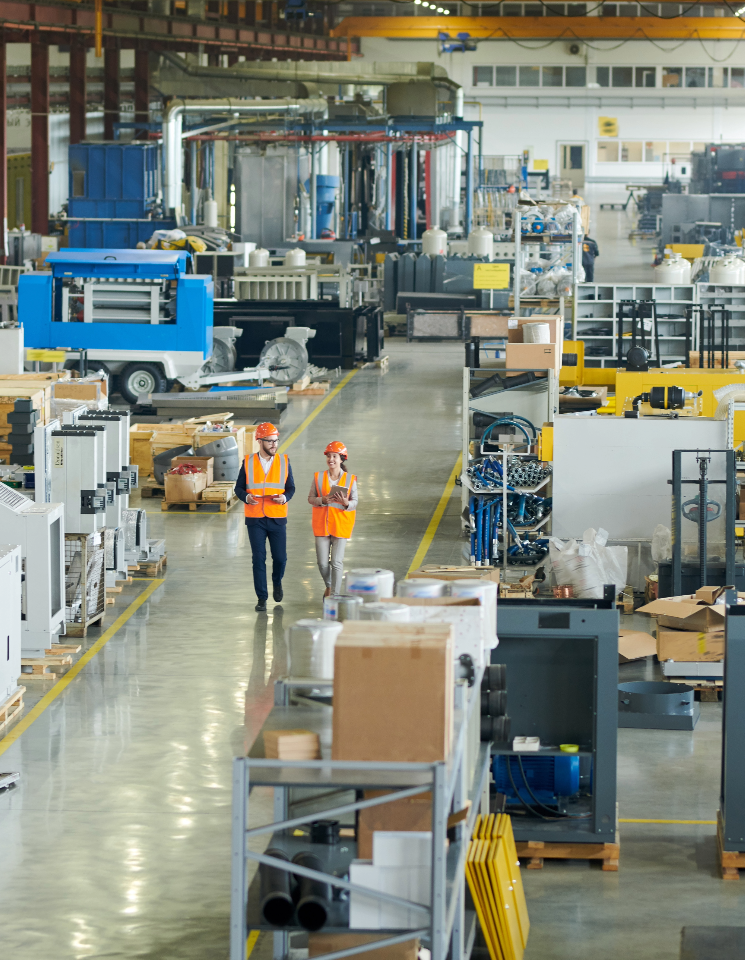
Maintenance excellence is all about achieving exemplary performance from physical assets at a reasonable cost. But what exactly is the "size of the prize" when investing in maintenance excellence? To understand this, we need to examine two key factors: capacity and cost.
In today's industrial landscape, the efficiency and productivity of physical assets are critical factors for an organization's success. The debate over an organization's social or business mandates becomes irrelevant if these assets are unproductive. In this article, we will explore the concept of maintenance excellence and the substantial benefits it brings to organizations.
Capacity:
Capacity is a measure of how effectively an asset is utilized. It can be calculated as follows:
Capacity = Availability × Use × Process Rate × Quality Rate
When equipment is available, in use, operates at the desired speed, and produces the desired quality and yield, it achieves the required maintenance output.
Cost:
The cost of maintenance can vary significantly based on various factors such as the working environment, available resources, equipment age, operating standards, and technology. One fundamental truth is that a breakdown maintenance strategy is far more costly than planned or preventive maintenance.
Create a Free Account to maintain your Assets
Here's a rule of thumb to estimate cost-saving potential in an industrial environment:
- Predictive, Preventive, Planned Maintenance = $1
- Unplanned, Unscheduled Maintenance = $1.5
- Breakdown Maintenance = $3
In other words, investing in planned and preventive maintenance now saves significantly more than dealing with breakdowns later. Emergency and breakdown maintenance is costlier for several reasons:
- Production interruptions
- Unprepared work sites
- Pulling skilled workers from their current tasks
- Hiring contractors and renting equipment
- Rushing to acquire materials
- Overtime work
- Lack of clear plans or drawings.
To illustrate, let's consider an annual maintenance budget of $100 million, with 50% planned, 30% unplanned, and 20% breakdown work. The cost breakdown would be:
- Planned Work Costs: $32 million
- Unplanned Work Costs: $29 million
- Emergency Work Costs: $39 million
Now, if we improve maintenance to 60% planned, 25% unplanned, and 15% breakdown, the costs become:
- Planned Work Costs: $39 million
- Unplanned Work Costs: $24 million
- Emergency Work Costs: $29 million.
This improvement leads to a potential savings of $8 million.
In conclusion, investing in maintenance excellence is not just about meeting mandates; it's a strategic move that can significantly impact an organization's bottom line. By minimizing breakdowns and maximizing planned, preventive, and predictive work, organizations can unlock substantial cost savings and enhance overall efficiency. Additionally, in today's world, it's crucial to consider the environmental impact of assets throughout their lifecycle, further emphasizing the need for sustainable "green" thinking in asset management.
