Key Performance Metrics for Facility Management
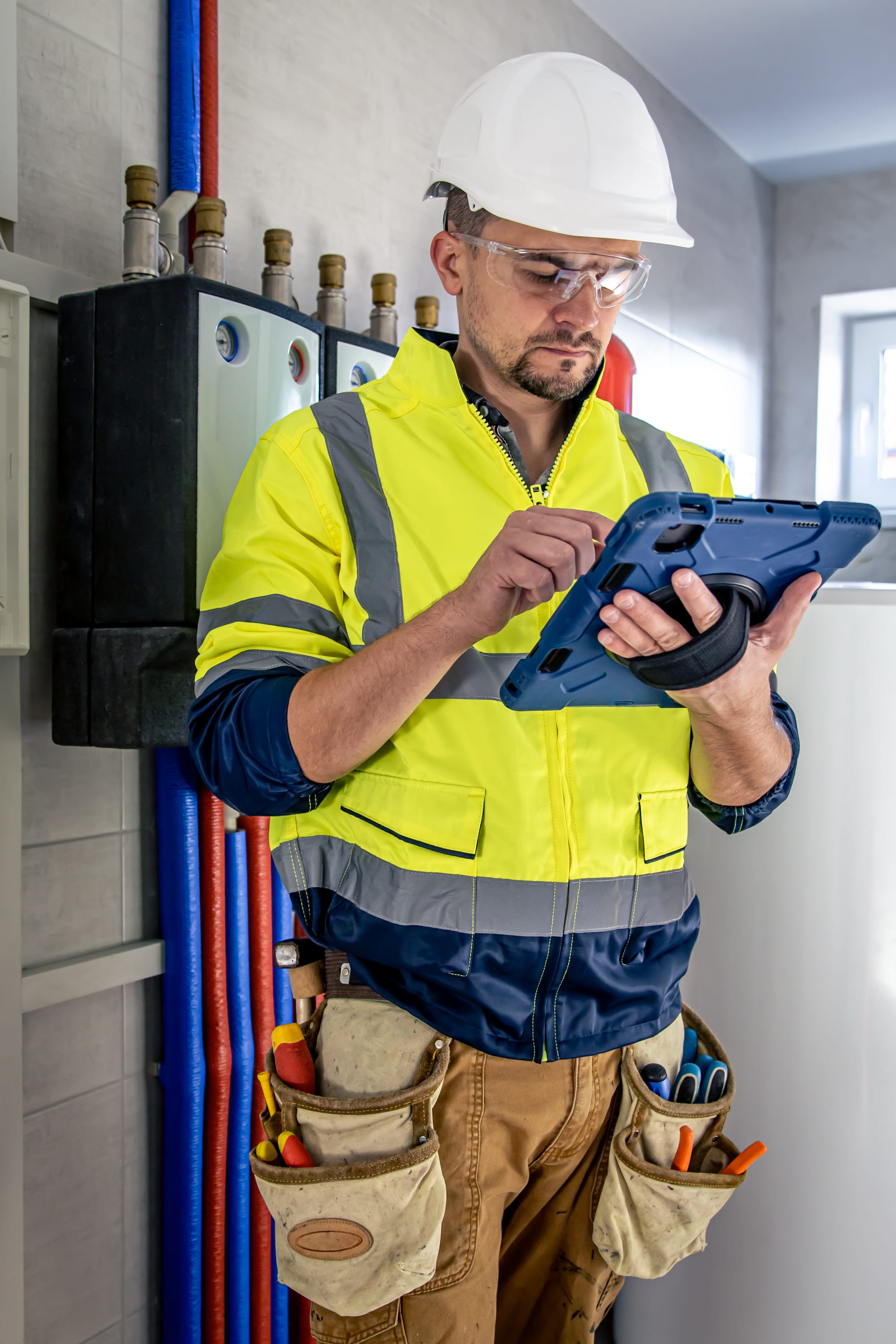
Effective facility management relies on measurable Key Performance Indicators (KPIs) to track efficiency, optimize maintenance budgets, and improve the overall condition of buildings. While many metrics exist, a concise set of performance indicators helps facility managers make data-driven decisions. Below, we explore some of the most widely discussed KPIs in the literature.
1. Maintenance Efficiency: Tracking Facility Upkeep
One of the core responsibilities of facility management is to balance maintenance costs while ensuring reliability. Maintenance efficiency is often measured through preventive vs. corrective maintenance expenditures.
- Preventive Maintenance: Scheduled maintenance to prevent sudden breakdowns.
- Corrective Maintenance: Repairs done after a failure occurs.
The Importance of Maintenance Efficiency Indicator (MEI)
To assess how well a facility manages its maintenance budget, the Maintenance Efficiency Indicator (MEI) is used. MEI helps facility managers:
Evaluate maintenance performance
✔ Optimize maintenance spending
✔ Support strategic decision-making
Since preventive maintenance can be difficult to quantify, MEI provides a standardized method to track and improve efficiency.
2. Replacement Efficiency: Measuring Long-Term Asset Renewal
Beyond maintenance, facilities must also plan for asset replacements. Equipment and infrastructure have a limited lifespan, and replacements are essential to maintain operational efficiency.
One way to measure replacement performance is through the Capital Renewal Index (CRI) which is the ratio of Annual Capitol Renewal to the Current Replacement Value.
- Capital Renewal: The yearly investment made to replace aging systems.
- CRV (Current Replacement Value): The cost to restore the facility to a “like-new” condition.
By tracking this ratio, facility managers can determine whether they are investing enough in asset replacement or if future costs will escalate due to aging infrastructure.
3. Facility Condition Index (FCI): Assessing the Overall Facility Health
The Facility Condition Index (FCI) is one of the most widely used metrics for determining a facility’s condition.
FCI is the ratio of the maintenance deficiency cost to the the current replacement value.
- Maintenance Deficiency Cost: Total cost of pending maintenance and repair work.
- CRV (Current Replacement Value): The estimated cost to replace the facility completely.
Interpreting FCI Values
- FCI ≤ 5% → Facility in Good Condition
- FCI 5%-10% → Facility in Fair Condition
- FCI > 10% → Facility in Poor Condition
Higher FCI values indicate a deteriorating facility, requiring urgent repairs or renewal.
How CMMS Helps Improve FCI
A Computerized Maintenance Management System (CMMS) like MaintainNow can track deficiencies and provide real-time insights into facility conditions. Automated preventive maintenance schedules help reduce backlog maintenance costs and lower the FCI over time.
4. Functional Space Index: Maximizing Space Utilization
Beyond monetary metrics, a facility’s performance also depends on how efficiently it utilizes available space. The Functional Space Index measures:
- The amount of usable space
- The quality and suitability of spaces
- Under-utilized or overcrowded areas
For example, in Schools, ffices, and Hospitals, space utilization impacts:
- Student performance (schools)
- Employee productivity (offices)
- Patient comfort and efficiency (hospitals)
By comparing existing space against industry standards, facility managers can reconfigure layouts to maximize efficiency.
5. Indoor/Outdoor Environmental Quality (IOEQ): Enhancing Workplace Comfort
Indoor air quality, lighting, ventilation, and noise levels significantly impact occupant health and productivity. Poor Indoor Environmental Quality (IEQ) can lead to:
- ❌ Increased absenteeism
- ❌ Reduced worker performance
- ❌ Higher turnover rates
A study by Fowler et al. (2005) found that adverse indoor conditions increase financial burdens for organizations due to higher medical costs, sick leaves, and compensation claims.
How to Measure IEQ
Modern building assessment systems like LEED certification provide a standardized approach to measuring and improving environmental quality. Facility managers can leverage IoT sensors to track:
- ✅ Air quality (CO₂, VOC levels)
- ✅ Temperature and humidity
- ✅ Noise and lighting conditions
Integrating these data points into a CMMS platform allows for real-time monitoring and preventive actions to improve workplace conditions.
6. Absenteeism & User Perception: The Human Impact of Facility Conditions
Facility management is not just about technical maintenance but also user satisfaction. Poor working conditions can lead to:
- Higher absenteeism rates
- Decreased employee satisfaction
- Lower organizational confidence
Studies in educational facilities have found that a poor indoor environment reduces student performance, while in offices, poor workspace quality increases turnover rates.
How CMMS Can Address This
A CMMS system can incorporate:
✅ Employee satisfaction surveys linked to facility conditions
✅ Track absenteeism trends vs. facility maintenance
✅ Automate comfort-related maintenance requests (HVAC, lighting, workspace adjustments)
By addressing occupant concerns proactively, organizations can boost morale, reduce absenteeism, and improve overall facility performance.
Conclusion: Using KPIs for Smarter Facility Management
Measuring facility performance requires a balance between financial, technical, and user-centered metrics. By integrating KPIs like MEI, FCI, CRI, and Functional Space Index into a CMMS, facility managers can:
✅ Optimize maintenance budgets
✅ Extend asset lifespans
✅ Improve environmental conditions
✅ Enhance user satisfaction & productivity
With real-time data tracking, automated reports, and AI-driven insights, a modern CMMS system ensures that facility management becomes proactive, efficient, and cost-effective.