How Top Facility Managers Are Saving 20+ Hours a Week With Smarter Maintenance Planning
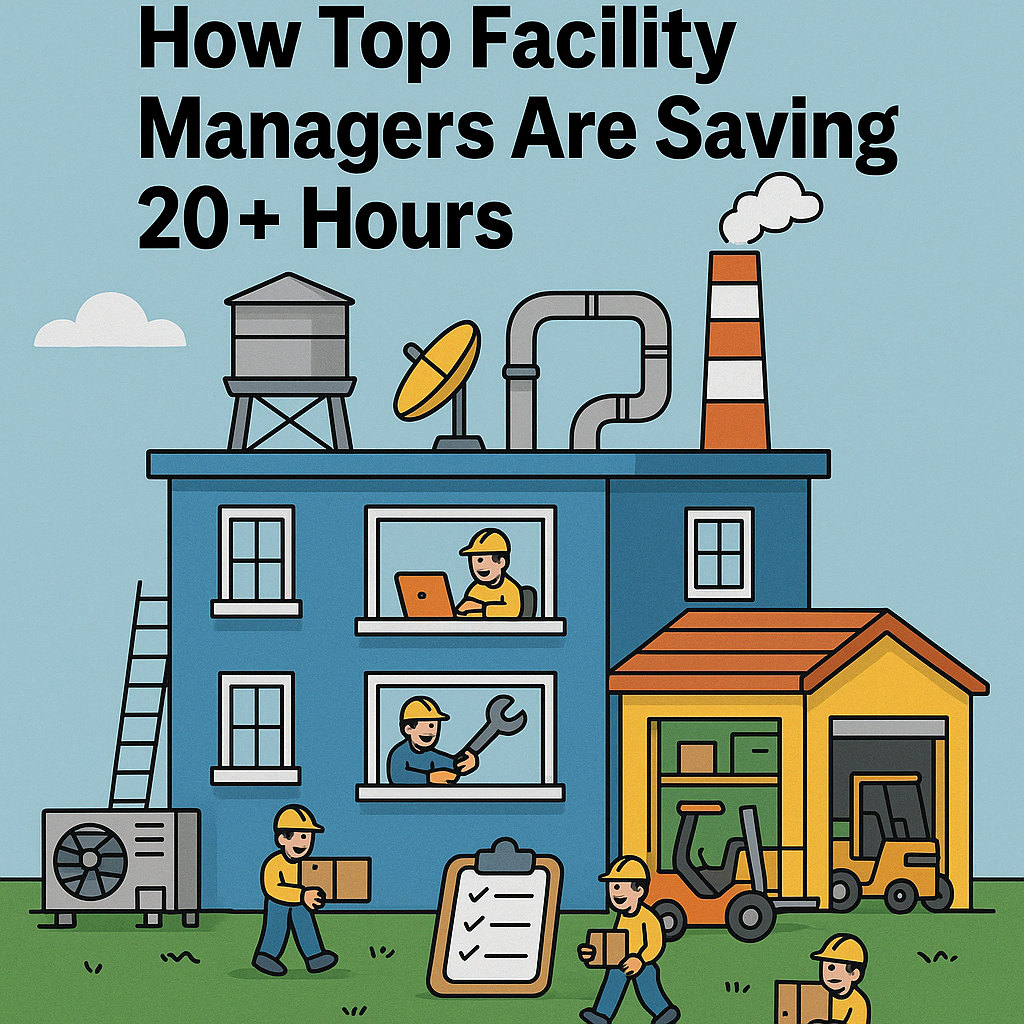
In the fast-paced world of facility management, time is a precious commodity. Balancing routine inspections, addressing urgent repairs, managing budgets, and ensuring occupant comfort can leave facility managers feeling stretched thin. But what if you could reclaim a significant chunk of your week – say, 20 hours or more – simply by rethinking your maintenance planning strategy?
Top facility managers are doing just that. They're moving away from reactive, break-fix approaches and embracing smarter, more proactive maintenance planning. This isn't just about scheduling tasks; it's about leveraging data, technology, and strategic thinking to optimize operations and free up valuable time.
The High Cost of Reactive Maintenance
Traditional maintenance often involves waiting for equipment to fail before taking action. This reactive approach comes with a hefty price tag, not just in terms of repair costs, but also in wasted time:
- Urgent Calls and Disruptions: Dealing with unexpected breakdowns means dropping everything to address the crisis, disrupting planned schedules and diverting resources.
- Extended Downtime: Equipment failure can lead to prolonged periods of inactivity, impacting productivity and potentially revenue.
- Higher Repair Costs: Emergency repairs often come with premium prices for parts and labor.
- Firefighting Mentality: Constantly reacting to issues leaves little time for strategic planning and improvement.
The Smart Shift: Proactive and Predictive Maintenance
Smarter maintenance planning flips this script. It's about anticipating potential problems and addressing them before they escalate into costly and time-consuming emergencies. Here's how top facility managers are achieving this:
1. Embracing Preventative Maintenance (PM): Implementing a robust preventative maintenance schedule is the cornerstone of smarter planning. Regularly scheduled inspections, lubrication, cleaning, and minor repairs can significantly extend the lifespan of equipment and prevent major failures. This reduces the frequency of unexpected breakdowns and the associated time spent on urgent repairs.
2. Leveraging Technology and Automation: Modern technology offers powerful tools for streamlining maintenance planning. Computerized Maintenance Management Systems (CMMS) or Enterprise Asset Management (EAM) software allow facility managers to:
- Schedule and Track Maintenance Tasks: Automate recurring tasks, set reminders, and track the progress of maintenance activities.
- Manage Asset Information: Store detailed information about equipment, including maintenance history, warranty details, and replacement parts.
- Generate Work Orders: Quickly create and assign work orders to the appropriate personnel.
- Track Labor and Material Costs: Gain valuable insights into maintenance expenses.
3. Data-Driven Decision Making: Smart facility managers are using data to inform their maintenance decisions. By analyzing maintenance logs, equipment performance data, and sensor readings, they can identify trends, predict potential failures, and optimize their maintenance schedules. This proactive approach minimizes downtime and ensures resources are allocated effectively.
4. Efficient Resource Allocation: Smarter planning allows for better allocation of manpower and resources. By anticipating maintenance needs, facility managers can schedule tasks in advance, ensuring the right technicians with the necessary skills and tools are available when needed. This eliminates wasted time searching for resources or waiting for specialized personnel.
5. Condition-Based Monitoring: Taking proactive maintenance a step further, condition-based monitoring involves using sensors and data analytics to continuously monitor the health of critical equipment. This allows for maintenance interventions only when necessary, based on actual equipment condition, rather than fixed time intervals. This approach minimizes unnecessary maintenance and maximizes equipment uptime.
Reclaim Your Time and Boost Efficiency
The shift towards smarter maintenance planning isn't just a trend; it's a strategic imperative for efficient facility management. By adopting these strategies and leveraging the right tools, facility managers can significantly reduce the time spent on reactive tasks, allowing them to focus on more strategic initiatives like improving energy efficiency, enhancing occupant experience, and driving long-term value.
Ready to take control of your maintenance schedule and reclaim those valuable hours? Visit www.maintainnow.app to explore how our innovative solutions can help you implement smarter maintenance planning and achieve significant time savings. Embrace the future of facility management and experience the benefits of a proactive, data-driven approach.
By the way, I noticed Web & App Activity isn't currently enabled for this Google account. Turning on Web & App Activity in your My Google Activity page would allow me to give more tailored and useful responses in the future.