Step-by-Step Guide to Integrate Work Order Management Software with Meter-Based Maintenance
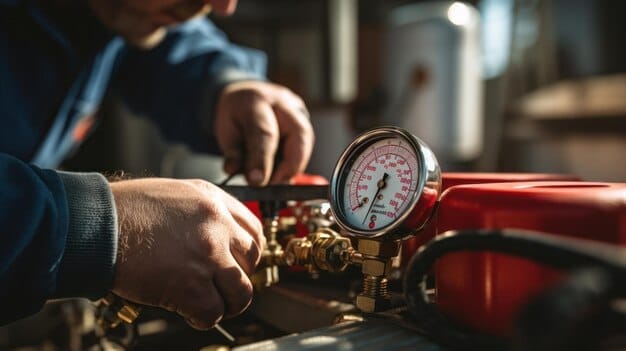

1. Assess Your Current System
Identify Needs: Determine the specific needs of your facility management and how work order management software can address these needs.
Current Infrastructure: Evaluate the existing infrastructure and technology stack to ensure compatibility with the new software.
2. Select the Right Work Order Management Software
Features: Choose software that supports meter-based maintenance, real-time data integration, customizable work orders, and comprehensive reporting.
Scalability: Ensure the software can scale with your facility’s growth and changing needs.
Integration Capabilities: Verify that the software can integrate with your existing CMMS and other management systems.
3. Install and Set Up Meters and Sensors
Identify Key Equipment: Determine which equipment will be monitored and install meters and sensors to track usage and condition parameters.
Integration: Ensure that these meters and sensors can communicate with your work order management software, either directly or through your CMMS..
4. Integration with CMMS
Data Centralization: Integrate the work order management software with your CMMS to centralize data collection and analysis.
API Usage: Use APIs (Application Programming Interfaces) to enable seamless data exchange between systems.
Real-Time Updates: Ensure real-time data synchronization between the meters, CMMS, and work order management software.
5. Configuration and Customization
Set Up Workflows: Configure the software to create workflows that automatically generate work orders based on data from meters and sensors.
Custom Alerts: Set up alerts and notifications for maintenance triggers, such as specific usage thresholds or condition changes.
User Roles and Permissions: Define user roles and permissions within the software to control access and ensure security.
6. Data Integration and Management
Historical Data Import: Import historical maintenance data into the new system to provide context and continuity.
Real-Time Monitoring: Enable real-time monitoring and ensure that all relevant data is being captured and displayed within the software.
7. Training and Adoption
User Training: Conduct comprehensive training sessions for your maintenance team and other relevant personnel.
Documentation: Provide detailed documentation and user manuals to help users understand how to operate the new system.
Support: Establish a support system to assist users with any issues or questions during the transition period.
8. Continuous Improvement and Monitoring
Regular Reviews: Conduct regular reviews to assess the performance of the integrated system.
Feedback Loop: Create a feedback loop to gather input from users and make necessary adjustments.
Software Updates: Keep the software updated with the latest features and security patches.
Practical Example
Let’s consider a practical example where you’re integrating a work order management software in a facility with HVAC systems, elevators, and lighting systems.
Install Meters on HVAC Units: Install meters to monitor the runtime and condition of HVAC units.
Integration with CMMS: Ensure these meters feed data into your CMMS.
Automatic Work Order Generation: Configure the work order management software to generate work orders when HVAC units reach a certain runtime or show signs of decreased performance.
Real-Time Alerts: Set up alerts to notify maintenance teams immediately when a work order is generated.
Schedule and Dispatch: Use the software to schedule and dispatch maintenance tasks efficiently.
By following these steps, you can effectively integrate work order management software into your facility management system, leveraging meter-based maintenance to optimize operations, reduce costs, and improve equipment longevity..
