Condition-Based Maintenance (CBM): Optimizing Equipment Performance
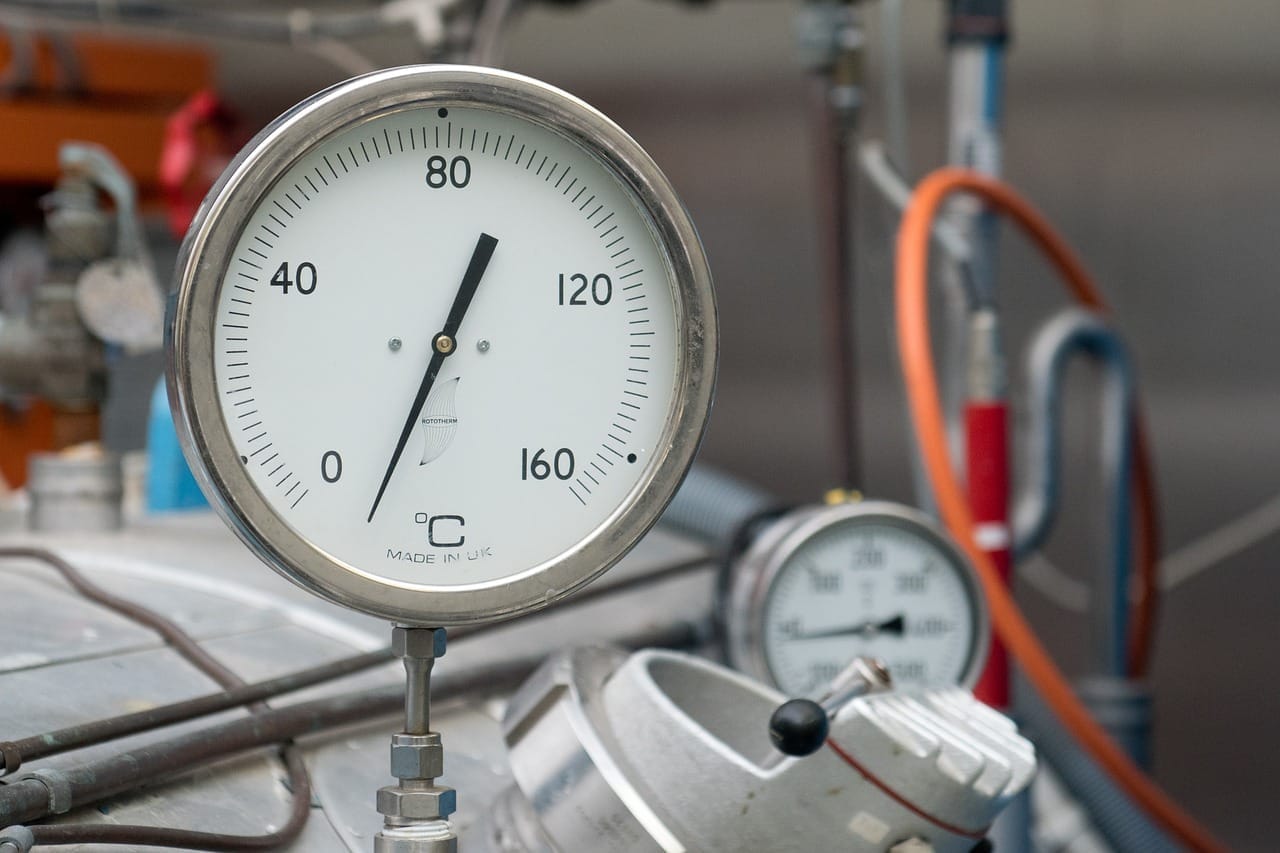
Introduction
In the ever-evolving landscape of industrial maintenance, Condition-Based Maintenance (CBM) has emerged as a cutting-edge approach, transforming the way organizations keep their machinery and equipment in optimal working condition. CBM, also known as predictive maintenance, is a sophisticated strategy that relies on real-time data and condition monitoring to make informed maintenance decisions. In this article, we will delve into the intricacies of CBM, its motivations, methods, and how it benefits various industries.
Understanding CBM
CBM was first introduced in 1975 with a single, clear objective: to maximize the effectiveness of maintenance decision-making. Traditional maintenance practices often follow a fixed schedule, leading to unnecessary downtime and resource wastage. CBM revolutionizes this paradigm by recommending maintenance actions based on real-time data collected through condition monitoring processes.
At the heart of CBM lies the concept that equipment has a lifecycle, and its health can be gauged by monitoring various parameters such as vibration, temperature, lubricating oil quality, contaminants, and noise levels. The key motivation behind CBM is the recognition that approximately 99 percent of equipment failures are heralded by specific signs, conditions, or indications. By identifying these precursors, CBM aims to enhance equipment health management, reduce lifecycle costs, and avert catastrophic failures.
The Role of Condition Monitoring (CM)
Condition monitoring is the cornerstone of CBM, where equipment signals are continuously scrutinized using a range of sensors or indicators. The fundamental principle is to perform maintenance activities, such as repairs or replacements, only when needed or just before a failure is anticipated. This proactive approach not only saves time and resources but also minimizes the risk of unexpected downtime.
CM can be executed in two primary ways: online and offline. Online monitoring takes place while the equipment is in operation, whereas offline monitoring occurs when the equipment is idle. Additionally, CM can be conducted either periodically, at scheduled intervals, or continuously, with real-time data analysis.
CM Techniques and Examples
CBM employs a variety of condition monitoring techniques, each tailored to different types of equipment. Here are some prominent CM techniques along with examples of their applications:
Vibration Monitoring: Vibration monitoring is particularly useful for rotating equipment, such as motors and turbines. By analyzing vibrations, CBM systems can detect irregularities that may indicate impending failures. For example, excessive vibration in a motor's bearings can signal potential problems, allowing maintenance teams to intervene before a breakdown occurs.
Sound or Acoustic Monitoring: This technique is closely related to vibration monitoring but focuses on the sounds emitted by equipment. It's used in applications like monitoring the performance of industrial pumps. Unusual sounds can signify issues such as cavitation or blockages, prompting timely maintenance.
Oil-Analysis or Lubricant Monitoring:
In this method, the condition of lubricating oil is evaluated to determine its quality and suitability for further use. For instance, in an aircraft engine, oil analysis can reveal wear conditions of internal components and provide crucial insights into engine health.
Other CM Techniques:
These encompass electrical monitoring (detecting changes in properties like resistance), temperature monitoring (critical for electric and electronic components), physical condition monitoring (identifying physical changes like cracks and corrosion), and performance monitoring (predicting problems based on parameters like pressure and flow rate).
Maintenance Decision Making in CBM
Maintenance decision-making within the CBM program can be categorized into two key phases: diagnosis and prognosis.
Diagnosis:
This phase involves identifying the source of a fault and providing early warnings to engineers when equipment operates abnormally. For example, a CBM system may detect unusual electrical resistance in a motor, prompting further inspection.
Prognosis:
Prognosis goes a step further by estimating or predicting when a failure may occur. This helps organizations determine the right time for preventive maintenance just before equipment failure is likely, ensuring maximum utilization.
Conclusion
Condition-Based Maintenance is at the forefront of modern maintenance practices, enabling industries to optimize equipment performance, reduce downtime, and cut maintenance costs. By harnessing the power of condition monitoring techniques and data-driven decision-making, CBM is helping organizations stay competitive in an increasingly demanding market. Embracing CBM can lead to improved reliability, extended equipment lifecycles, and enhanced operational efficiency across various sectors, from manufacturing to aviation. As technology continues to advance, CBM will undoubtedly play an even more pivotal role in shaping the future of maintenance strategies.
