Are Your Work Orders Sabotaging Your Facility? 5 Common Mistakes & How to Fix Them Fast
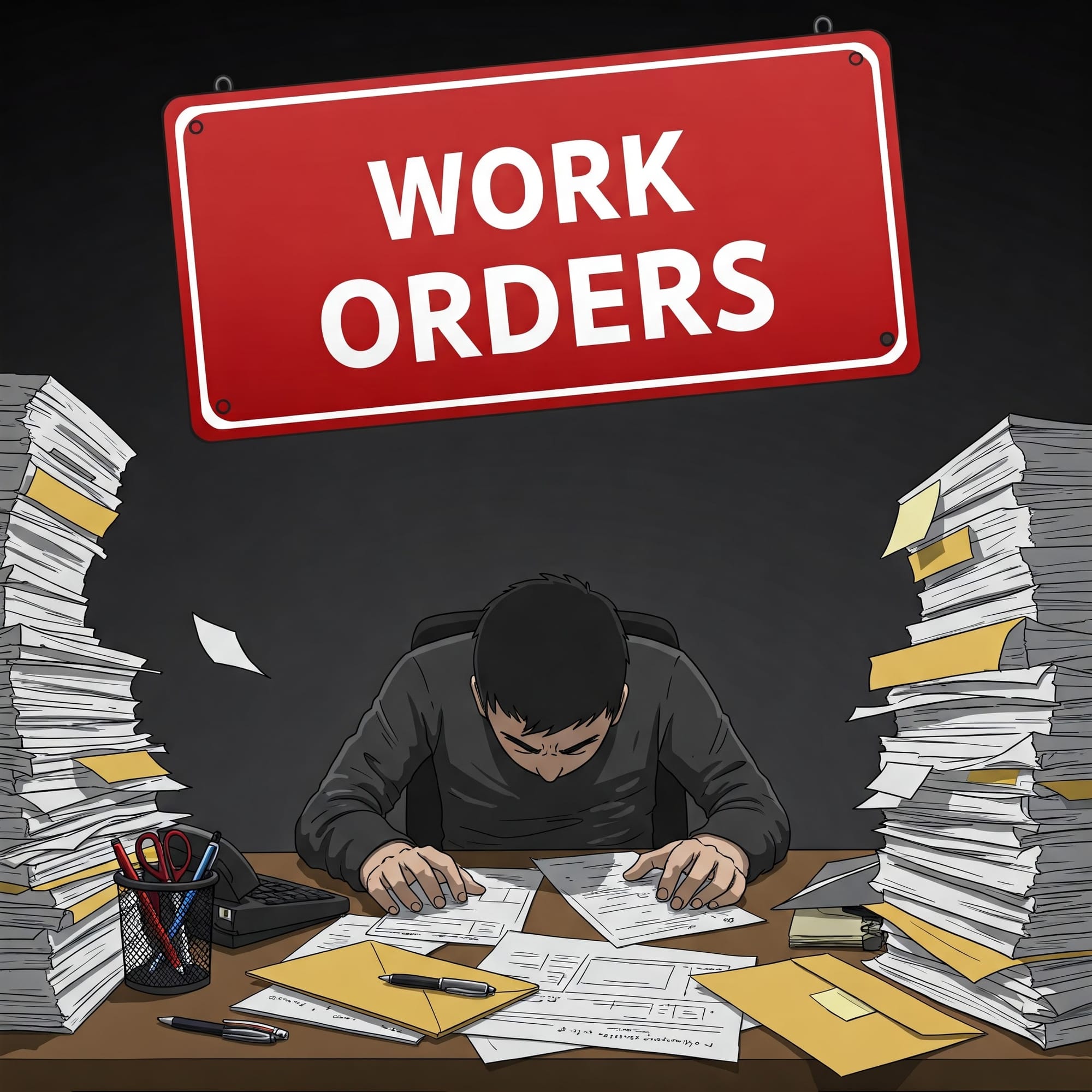
Work orders. They're the backbone of facility maintenance, the system meant to bring order to the chaos of repairs, requests, and routine upkeep. But what if the way you're handling them is actually hindering your operations, increasing downtime, and costing you money?
Many facilities fall into common traps with their work order management. The good news? These mistakes are fixable. Let's look at five frequent pitfalls and the best practices you can implement today – potentially supercharged by the right maintenance software.
Mistake #1: The Vague Request – "Just Fix It!"
The Problem: Work orders lack crucial details. "Pump broken" or "AC not working" leaves maintenance technicians guessing. Which pump? Where is it? What's the specific issue? This leads to wasted time tracking down information, potential misdiagnoses, and delays in critical repairs.
The Fix (Best Practice): Implement standardized work order forms (digital is best!) that require essential information:
- Specific asset tag/ID and location.
- Detailed description of the problem.
- Requester name and contact info.
- Date reported.
- Initial priority level (see Mistake #2).
- Any relevant safety notes.
Keywords: work order
, maintenance technician
, repair request
, asset management
Mistake #2: All Priorities Are Equal (Meaning None Are)
The Problem: Your work order system doesn't effectively prioritize tasks. Emergency corrective maintenance gets lost in a sea of routine requests, or minor issues jump the queue based on who shouts loudest. This directly impacts operational downtime and safety.
The Fix (Best Practice): Establish clear, consistent priority levels (e.g., Critical, High, Medium, Low) based on predefined criteria:
- Critical: Immediate safety risk or total operational shutdown.
- High: Significant operational impact or potential for rapid deterioration.
- Medium: Important but not immediately impacting core operations (e.g., scheduled preventive maintenance).
- Low: Minor issues, cosmetic repairs. Train staff on how to assign priorities and review them regularly.
Keywords: work order system
, prioritization
, downtime
, corrective maintenance
, preventive maintenance (PM)
Mistake #3: The Black Hole of Maintenance History
The Problem: Using paper, spreadsheets, or basic tools means there's no easily accessible history for your assets. You can't quickly see past repairs, identify recurring issues, or track parts used. Technicians fly blind, and facility managers lack data for informed decisions.
The Fix (Best Practice): Implement robust maintenance tracking. Every work order should become part of an asset's permanent digital record, capturing:
- Completion date and time.
- Technician(s) assigned.
- Time spent.
- Parts and costs associated.
- Detailed notes on the resolution. This history is invaluable for troubleshooting and asset management.
Keywords: maintenance tracking
, asset management
, facility manager
, maintenance history
Mistake #4: Preventive Maintenance Takes a Backseat
The Problem: Reactive "firefighting" consumes all your resources. Preventive maintenance (PM) tasks, crucial for preventing breakdowns, get constantly deferred. This seems like saving time but inevitably leads to more frequent, more expensive emergency repairs and higher overall maintenance costs.
The Fix (Best Practice): Treat PM work orders generated by your maintenance schedule with the same importance as repair requests. Use a system that automatically generates and helps schedule PMs, ensuring they don't get forgotten. Proactive maintenance always pays off.
Keywords: preventive maintenance (PM)
, maintenance schedule
, maintenance costs
, reactive maintenance
Mistake #5: Flying Blind – Not Using Your Data
The Problem: You might be collecting work order information, but it sits unused. You aren't analyzing trends, tracking key performance indicators (KPIs) like mean time to repair (MTTR), or identifying problem assets that drain resources.
The Fix (Best Practice): Leverage your work order data! Regularly review reports on:
- Work order backlog and completion rates.
- Maintenance costs per asset or department.
- Common failure points.
- Technician performance. This data empowers strategic maintenance management decisions.
Keywords: data analysis
, maintenance management
, KPIs
, reporting
Stop Sabotaging, Start Streamlining with MaintainNow CMMS
Fixing these issues manually can feel overwhelming. That's where a modern CMMS (Computerized Maintenance Management System) becomes essential.
Platforms like MaintainNow CMMS are specifically designed to embed these best practices directly into your workflow. With MaintainNow, you can:
- Standardize: Create detailed, required-field work order templates.
- Prioritize: Easily assign and visualize task priorities.
- Track Everything: Automatically build comprehensive asset histories.
- Automate PMs: Set up recurring maintenance schedules effortlessly.
- Analyze: Generate insightful reports with just a few clicks.
Getting started with a user-friendly CMMS like MaintainNow is often faster and simpler than you imagine, putting powerful, efficient work order management tools directly into your hands and helping you keep your facility in top order.