5 Costly Maintenance Mistakes Facility Managers Make (And How to Fix Them)
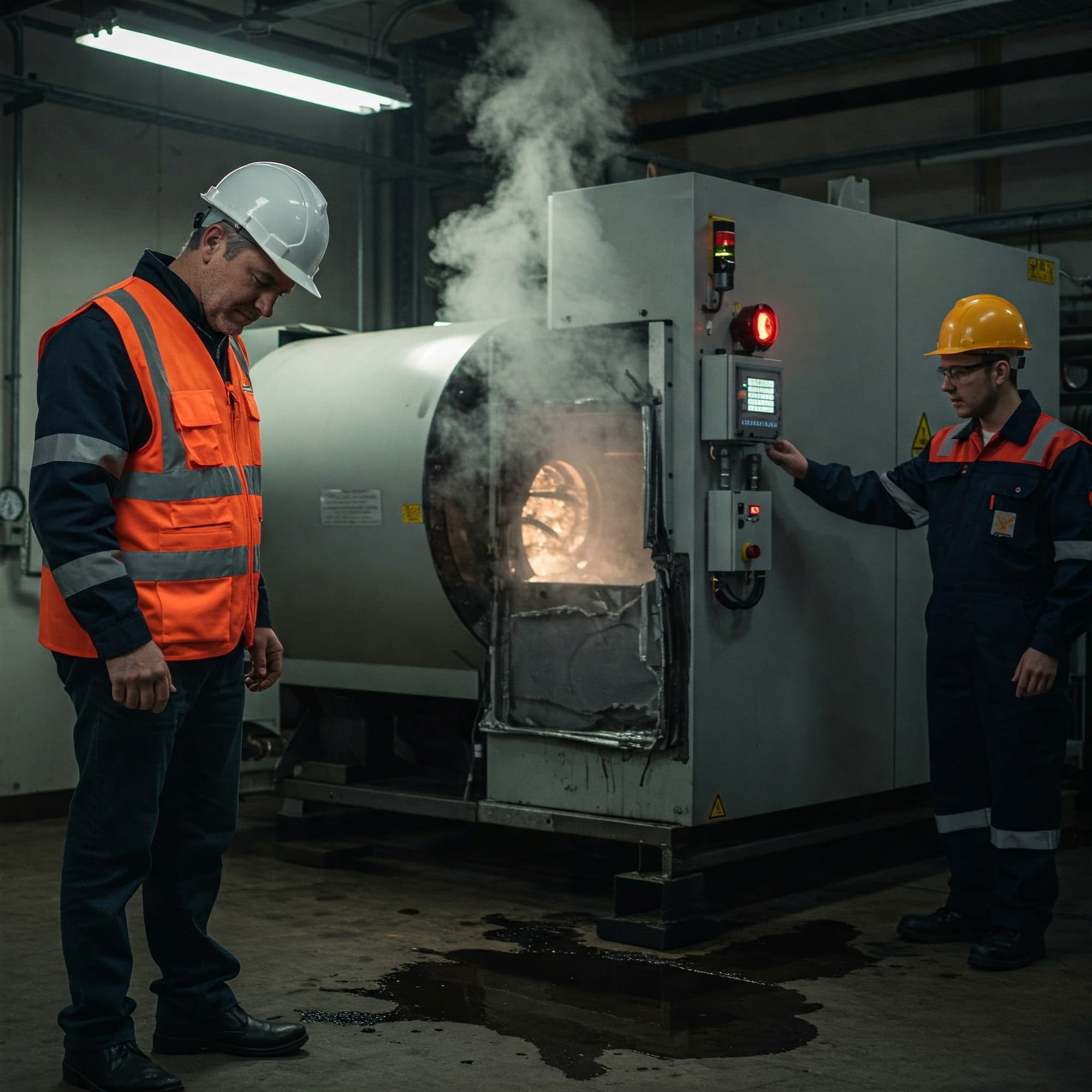
Facility management is a complex balancing act. Juggling budgets, schedules, compliance, and unexpected breakdowns requires strategic planning and execution. Unfortunately, even experienced managers can fall into common traps that lead to inflated costs, increased downtime, and unnecessary stress.
Are you making any of these costly maintenance mistakes? Let's explore five common pitfalls and, more importantly, how to fix them to optimize your operations and protect your bottom line.
1. Over-Reliance on Reactive Maintenance ("Run-to-Failure")
The Cost: Waiting for equipment to break down before fixing it might seem like saving money upfront, but it's often the most expensive strategy. Unexpected failures lead to emergency repairs (often at premium rates), unplanned downtime disrupting operations, potential safety hazards, and shorter asset lifespans.
The Fix: Shift towards a proactive maintenance strategy. Implement a robust preventive maintenance (PM) schedule based on manufacturer recommendations, usage patterns, and historical data. This involves regular inspections, lubrication, cleaning, and parts replacement before failure occurs. Utilizing effective maintenance software can automate scheduling, track task completion, and ensure critical PMs aren't missed.
2. Inefficient Inventory Management
The Cost: Not having the right spare part when needed means extended downtime while you scramble to order it (often expedited at extra cost). Conversely, overstocking ties up capital in unnecessary inventory, requires storage space, and increases the risk of parts becoming obsolete or damaged.
The Fix: Implement a system for tracking spare parts inventory accurately. Know what you have, where it is, and when to reorder. A good CMMS often includes inventory management modules that track usage, set reorder points, and link parts to specific assets and work orders. This ensures technicians have the parts they need without wasteful overstocking.
3. Poor Record-Keeping and Data Utilization
The Cost: Without accurate records of maintenance history, repairs, costs, and asset performance, you're flying blind. You can't identify recurring problems, track maintenance spending effectively, make informed decisions about repairs vs. replacement, or demonstrate compliance easily.
The Fix: Digitize your maintenance records. Implement a system where all work orders, PM tasks, parts used, labor hours, and costs are meticulously logged against specific assets. Modern CMMS solutions excel at this, providing a centralized database and reporting tools. Analyzing this data helps identify trends, optimize PM schedules, justify budgets, and make data-driven decisions for long-term savings.
4. Neglecting Technician Training and Skill Development
The Cost: An undertrained or improperly skilled maintenance team can lead to incorrect repairs, longer repair times, safety incidents, and damage to equipment. Relying on a single "expert" for critical systems also creates a bottleneck and risk if that person is unavailable.
The Fix: Invest in ongoing training for your maintenance staff. Ensure they are up-to-date on new equipment, technologies, and safety procedures. Cross-training team members builds redundancy and flexibility. A CMMS can help by storing standard operating procedures (SOPs), safety checklists, and equipment manuals directly within work orders, providing easy access to critical information in the field.
5. Ignoring Predictive Maintenance (PdM) Opportunities
The Cost: While preventive maintenance is crucial, predictive maintenance takes it a step further by using condition-monitoring tools (like vibration analysis, thermography, oil analysis) to predict when a failure is likely to occur. Ignoring these technologies means missing opportunities to perform maintenance at the optimal time, just before failure, maximizing asset life and minimizing intervention costs.
The Fix: Explore and selectively implement PdM technologies where appropriate for critical assets. Integrate the data and alerts from these tools into your overall maintenance strategy. While not a replacement for PM, PdM adds another layer of intelligence. A flexible platform like MaintainNow can help integrate data points and trigger work orders based on condition alerts, moving you towards a truly optimized maintenance program.
Stop Reacting, Start Maintaining Strategically
Avoiding these common mistakes isn't just about saving money; it's about creating a safer, more reliable, and more efficient facility. By shifting from reactive fixes to proactive strategies, optimizing inventory, leveraging data, investing in your team, and exploring predictive technologies, you can significantly improve your maintenance outcomes. Implementing a robust CMMS is often the foundational step in making these improvements a reality.
Facility management is a complex balancing act. Juggling budgets, schedules, compliance, and unexpected breakdowns requires strategic planning and execution. Unfortunately, even experienced managers can fall into common traps that lead to inflated costs, increased downtime, and unnecessary stress.
Are you making any of these costly maintenance mistakes? Let's explore five common pitfalls and, more importantly, how to fix them to optimize your operations and protect your bottom line.
1. Over-Reliance on Reactive Maintenance ("Run-to-Failure")
The Cost: Waiting for equipment to break down before fixing it might seem like saving money upfront, but it's often the most expensive strategy. Unexpected failures lead to emergency repairs (often at premium rates), unplanned downtime disrupting operations, potential safety hazards, and shorter asset lifespans.
The Fix: Shift towards a proactive maintenance strategy. Implement a robust preventive maintenance (PM) schedule based on manufacturer recommendations, usage patterns, and historical data. This involves regular inspections, lubrication, cleaning, and parts replacement before failure occurs. Utilizing effective maintenance software can automate scheduling, track task completion, and ensure critical PMs aren't missed.
2. Inefficient Inventory Management
The Cost: Not having the right spare part when needed means extended downtime while you scramble to order it (often expedited at extra cost). Conversely, overstocking ties up capital in unnecessary inventory, requires storage space, and increases the risk of parts becoming obsolete or damaged.
The Fix: Implement a system for tracking spare parts inventory accurately. Know what you have, where it is, and when to reorder. A good CMMS often includes inventory management modules that track usage, set reorder points, and link parts to specific assets and work orders. This ensures technicians have the parts they need without wasteful overstocking.
3. Poor Record-Keeping and Data Utilization
The Cost: Without accurate records of maintenance history, repairs, costs, and asset performance, you're flying blind. You can't identify recurring problems, track maintenance spending effectively, make informed decisions about repairs vs. replacement, or demonstrate compliance easily.
The Fix: Digitize your maintenance records. Implement a system where all work orders, PM tasks, parts used, labor hours, and costs are meticulously logged against specific assets. Modern CMMS solutions excel at this, providing a centralized database and reporting tools. Analyzing this data helps identify trends, optimize PM schedules, justify budgets, and make data-driven decisions for long-term savings.
4. Neglecting Technician Training and Skill Development
The Cost: An undertrained or improperly skilled maintenance team can lead to incorrect repairs, longer repair times, safety incidents, and damage to equipment. Relying on a single "expert" for critical systems also creates a bottleneck and risk if that person is unavailable.
The Fix: Invest in ongoing training for your maintenance staff. Ensure they are up-to-date on new equipment, technologies, and safety procedures. Cross-training team members builds redundancy and flexibility. A CMMS can help by storing standard operating procedures (SOPs), safety checklists, and equipment manuals directly within work orders, providing easy access to critical information in the field.
5. Ignoring Predictive Maintenance (PdM) Opportunities
The Cost: While preventive maintenance is crucial, predictive maintenance takes it a step further by using condition-monitoring tools (like vibration analysis, thermography, oil analysis) to predict when a failure is likely to occur. Ignoring these technologies means missing opportunities to perform maintenance at the optimal time, just before failure, maximizing asset life and minimizing intervention costs.
The Fix: Explore and selectively implement PdM technologies where appropriate for critical assets. Integrate the data and alerts from these tools into your overall maintenance strategy. While not a replacement for PM, PdM adds another layer of intelligence. A flexible platform like MaintainNow can help integrate data points and trigger work orders based on condition alerts, moving you towards a truly optimized maintenance program.
Stop Reacting, Start Maintaining Strategically
Avoiding these common mistakes isn't just about saving money; it's about creating a safer, more reliable, and more efficient facility. By shifting from reactive fixes to proactive strategies, optimizing inventory, leveraging data, investing in your team, and exploring predictive technologies, you can significantly improve your maintenance outcomes. Implementing a robust CMMS is often the foundational step in making these improvements a reality.